Create guidelines and design software for screw turbines
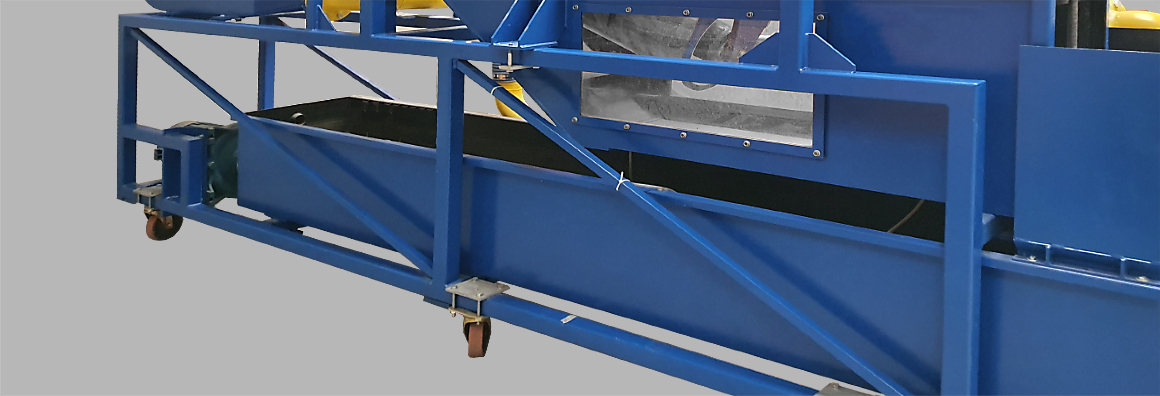
With Pelfa Group we collaborated in conceiving and developing a new software for designing hydroelectric power screw turbines. The objective was to increase its efficiency by working on the design criteria as well as the automatic optimization logics for the adjustment of operating parameters. Without significant references in scientific literature, we were able to generate the know-how necessary to identify the first guidelines, integrating actual data and laboratory data, defining an efficient numerical model and then implementing the design software.
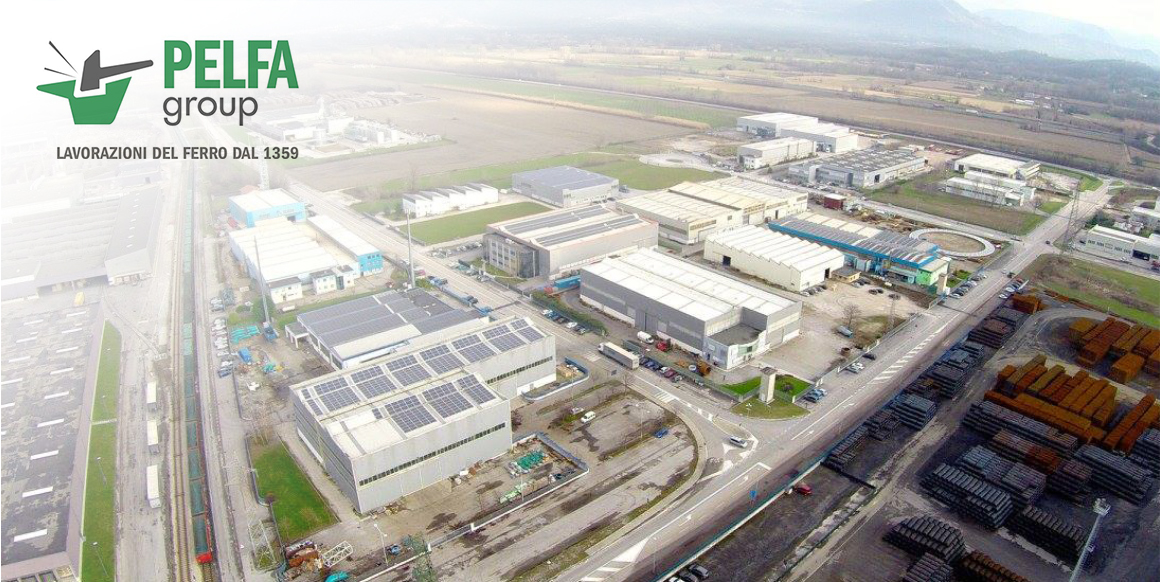
Customer: Pelfa Group
Pelfa Group is specialized in manufacturing turnkey installations, machines, mechanical components and electro-welded pieces for different industrial sectors. Over the last few years, the company has also specialized in the energy sector, including wind power, offshore, oil&gas, nuclear and especially hydroelectric, for which complete hydroelectric systems are made, including Francis, Kaplan, Pelton and screw turbines.
Advantech TIME research projects
The screw turbines are of particular interest in order to use the energy in small waterfalls (3-4 m) with a flow rate that is also significantly variable over time. The water flows into the screw with different volumes between the two sides of the turbine and this unbalancing starts the machine. The work developed by its rotation is transformed into energy. After the first successful installations, Pelfa Group has decided to invest in the development of this machine, but the objective of reaching design and use optimization criteria clashed with the scarcity of validated guide line for its design and operation. From this point on, the need for the research project developed with Advantech TIME.
Phases to define guidelines and software
- Designing and building a small scale model of a screw turbine.
- Experimental activity on the model by testing different rotor geometries and variable working conditions (such as number of revolutions, geodesic heads, tilt of the turbine axis, upstream and downstream submersion level).
- Development of numerical models, obtained starting from laboratory data, towards the functional design of the machine and optimization of its working parameters.
- Monitoring performance of current systems in order to create a significant database and carrying out validation of numerical models.
- Developing a software to help systems analysis and design.
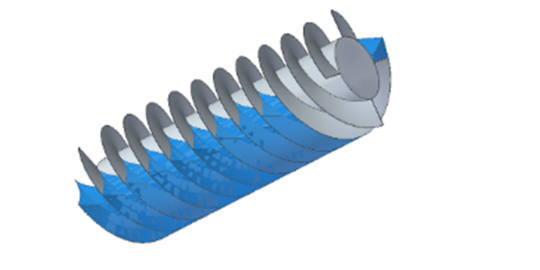
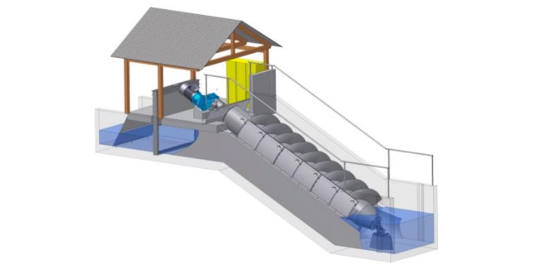

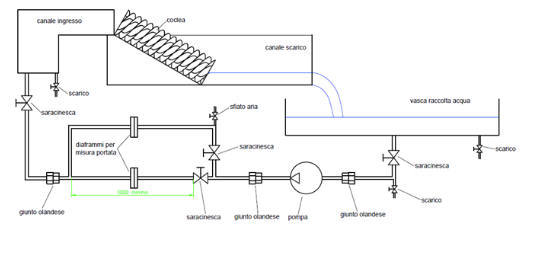
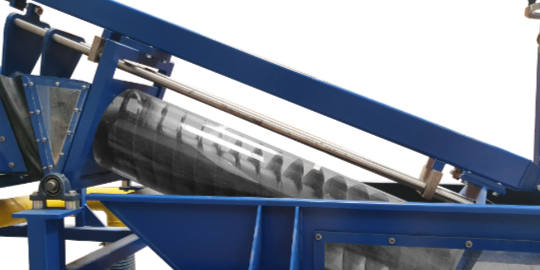