Analisi di fattibilità: geometrie per scambio termico
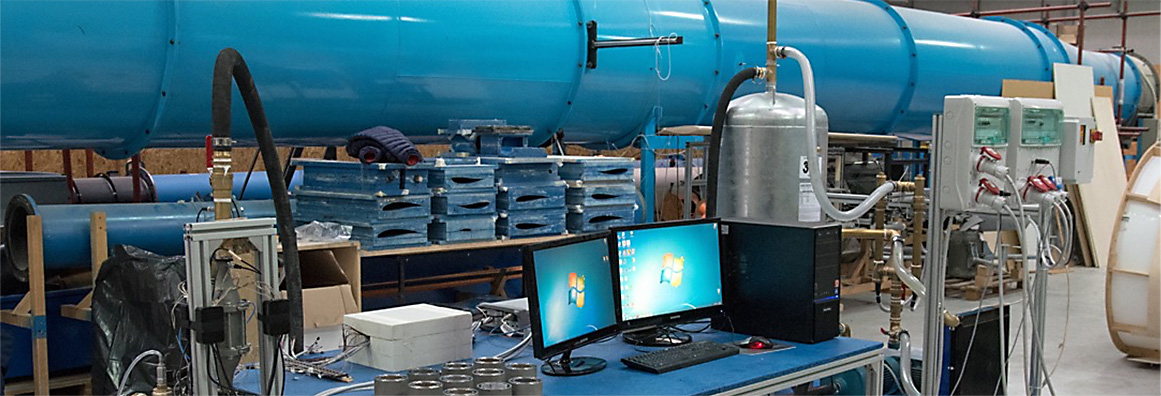
Per Wärtsilä Italia abbiamo condotto un’analisi di fattibilità sull’impiego di tecnologie di additive manufacturing per la realizzazione di soluzioni innovative per il raffreddamento di componenti di motore a combustione interna. L’additive manufacturing apre nuove possibilità per il design di geometrie di scambio termico ad alta efficienza perché consente assoluta libertà di forme e materiali.
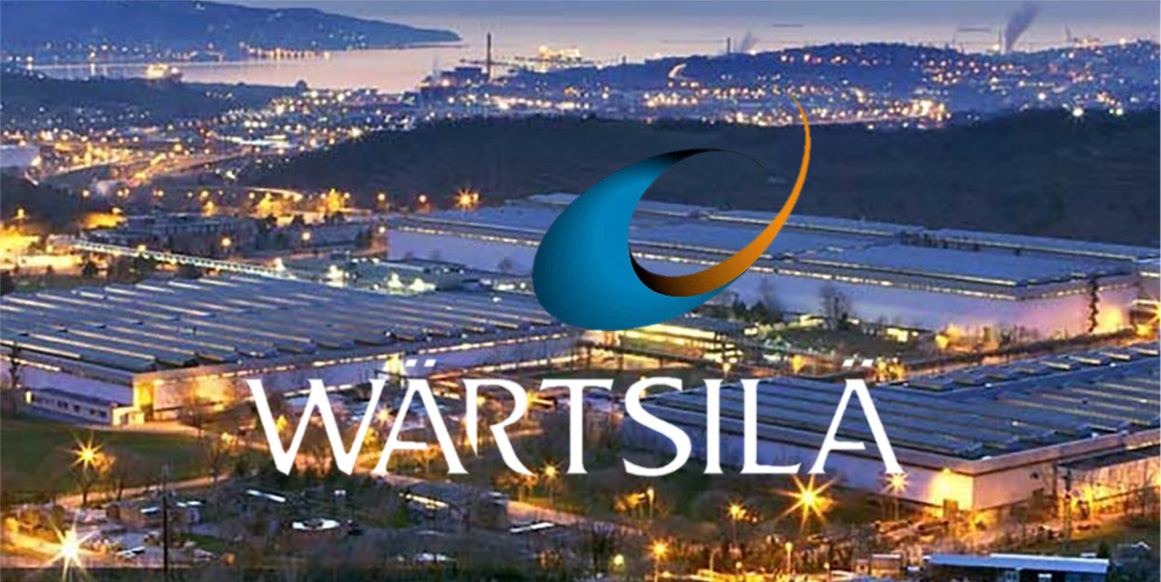
Cliente: Wärtsilä Italia
Wärtsilä Corporation è un’azienda finlandese leader nel fornire soluzioni tecnologiche intelligenti per generare energia nell’intero ciclo di vita degli impianti del settore marino e terrestre. Wärtsilä Italia è specializzata nella produzione di motori per uso navale, motori Diesel o bi-fuel, motori per generatori di corrente per centrali elettriche, motori per la propulsione e gruppi elettrogeni.
Progetto di ricerca Advantech TIME
È stato condotto un progetto di ricerca sull’impiego delle tecnologie di stampa 3D di manufatti metallici per produrre componenti di motore raffreddati mediante Selective Laser Melting (SLM) a partire da polveri metalliche. L’analisi di fattibilità, in stretta collaborazione con l’Università di Udine, era finalizzata a indagare le geometrie permesse dall’additive manufacturing, volte ad aumentare l’efficienza dei componenti, in termini di scambio termico accresciuto, dimensioni ridotte, compattezza aumentata, costi diminuiti, e impossibili da ottenere con le tecniche tradizionali. Essendo configurazioni fortemente innovative, è stato necessario procedere a un’approfondita analisi di caratterizzazione sperimentale del loro funzionamento e alla verifica delle performance attese.
Fasi dell’analisi di fattibilità
- Definizione della geometria base da testare fra quelle di maggiore interesse per il cliente e la sua applicazione finale.
- Definizione delle condizioni di esercizio, come carichi termici, temperature di esercizio, portate di refrigerante e perdite di carico ammissibili.
- Analisi di letteratura per identificare le soluzioni geometriche dei canali di raffreddamento in grado di massimizzare lo scambio termico e minimizzare le perdite di carico.
- Selezione geometrie da testare e studio FEM per la verifica dei carichi meccanici, disegno finale provini e stampa metallica.
- Parallelamente, ideazione, progetto, realizzazione e collaudo dell’impianto prova.
- Esecuzione dei test e individuazione delle geometrie più promettenti da indagare nel dettaglio con successiva attività.
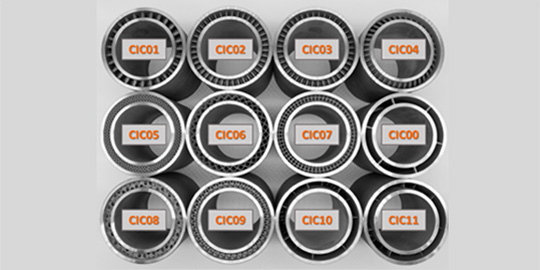
Esempio di geometrie indagate per un cilindro del motore a combustione interna oggetto dell’analisi di fattibilità
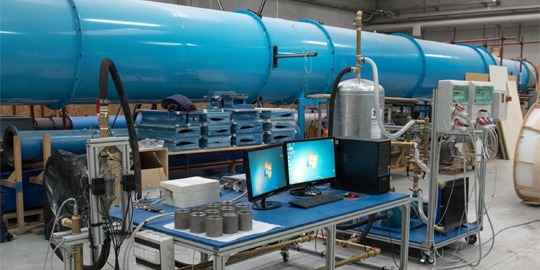
Impianto prova costruito appositamente per il progetto di ricerca
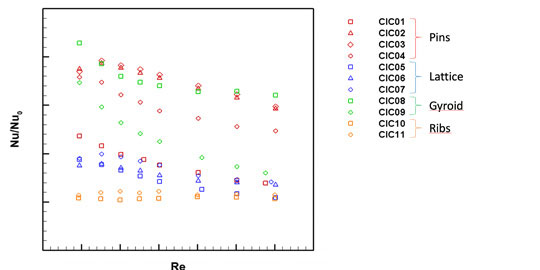
Misure di scambio termico per indagare la resa di diverse geometrie prodotte con SLM